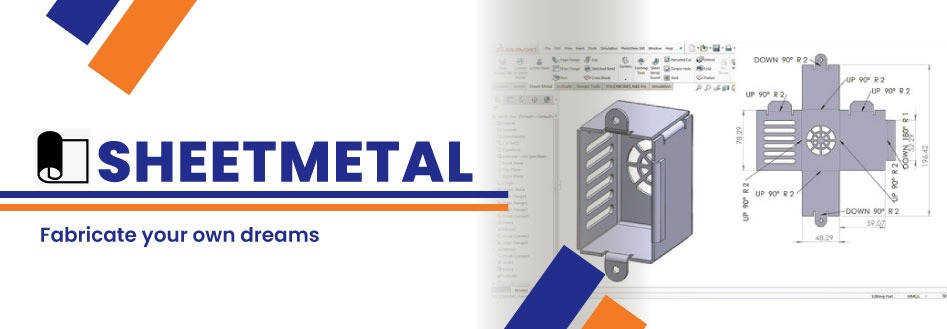
Sheetmetal Design Training in India
- Real-Time Experts Sessions
- LIVE Project
- Certification
- Affordable Fees
- Flexibility
- Placement Support
Sheet metal design plays an imperative role in the making of a strong backbone. A designer must have a distinct set of purposes and design strategies well-known to secure that part design is cost effective and can be easily manufactured. Function, attachment method, mechanical properties, and developed properties should be considered over before moving well into the design cycle. Tech Cluster is an institute which provides Sheet metal design training in Indore and offers chances to avail a great opportunity to learn the tool from basic to advanced level. Our expert faculties cover all the important factors of Sheet metal design Training for beginners and intermediates. With our expert guidance students can excel in their career and earn good. After which you can find good opportunities in MNC Industries like Eicher and other automobile industries.
Course Highlights:
Sheetmetal Design Foundation :
- Sheet metal Design Introduction
- Forming Basics
- Laser Cutting
- Tolerances
- Features
Duration :
- 20 Hours Theory
- 20 Hours Practical
- 20 Hours Project work
Technical Features:
Sheet metal Design Introduction
Sheet Metal Fabrication is the process of forming parts from a metal sheet by punching, cutting, stamping, and bending.
3D CAD files are converted into machine code, which controls a machine to precisely cut and form the sheets into the final part.
Sheet metal parts are known for their durability, which makes them great for end use applications (e.g. chassis). Parts used for low volume prototypes, and high volume production runs are most cost-effective due to large initial setup and material costs.
Because parts are formed from a single sheet of metal, designs must maintain a uniform thickness. Be sure to follow the design requirements and tolerances to ensure parts fall closer to design intent and cutting sheets of metal
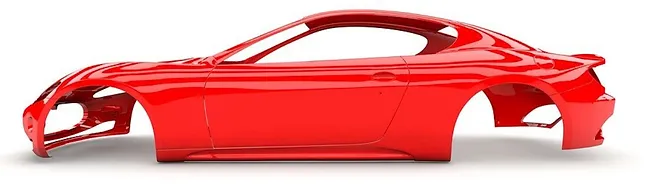
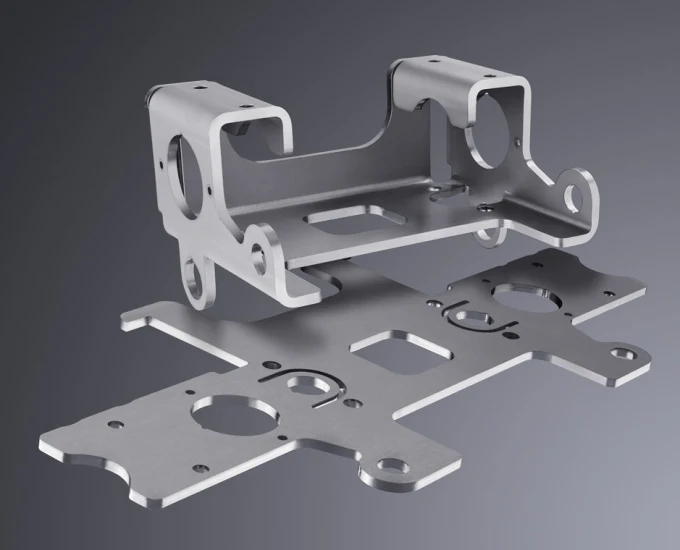
Forming Basics
- Bending – Sheet metal bending is an effective way of making products with different shapes used for different processes. It guarantees simplicity and it is an efficient way of forming new products. Here, you will know about sheet metal bending, its importance, and the methods needed for the process. Sheet metal bending is an operation that involves using forces to change the shape of a sheet. This is done to achieve the desired form or shape needed for a manufacturing process.
- K-Factor- The K-Factor in sheet metal working is the ratio of the neutral axis to the material thickness. When metal is bent the top section is going to undergo compression and the bottom section will be stretched. The line where the transition from compression to stretching occurs is called the neutral axis. The location of the neutral axis varies and is based on the material’s physical properties and its thickness. The K-Factor is the ratio of the Neutral Axis’ Offset and the Material Thickness.
- Bend Relief – In sheet metal, a bend relief is an incision cut along the sides of a planned bend. Though bend relief lengths and widths vary between projects, they all share a common goal: preventing tearing and part deformation during the bending process.
- Bend allowance – The Bend Allowance is defined as the material you will add to the actual leg lengths of the part in order to develop a flat pattern. The leg lengths are the part of the flange which is outside of the bend radius.
- Critical Dimensions-Some critical dimensions that need to be considered when setting up sheet metal in CAD software are sheet metal thickness, the k-factor and bend radius. One needs to check that these factors are consistent with the tooling that will be used in manufacturing.
- Wall Thickness- Parts need to maintain a uniform wall thickness throughout. Generally capabilities of of 0,9mm – 20mm in thickness are able to be manufactured from sheet (<3mm) or plate (>3mm) but this tolerance depends mainly on the part.
When considering sheet metal thickness, a single sheet with punches (holes) is a good rule of thumb. Some features such as countersinks are doable but counter bores and other machined features are difficult to produce as they require post machining.
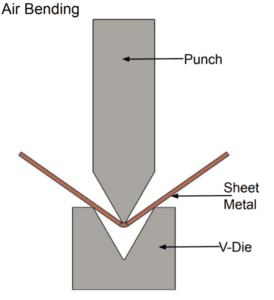
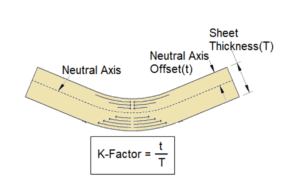
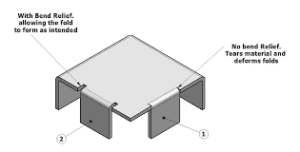
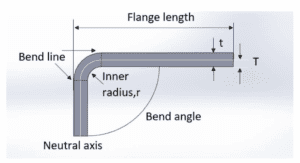
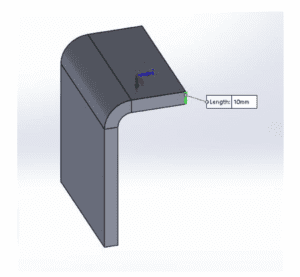
Laser Cutting
Laser cutting is a type of production that uses a laser to cut different metals. The laser has a high energy beam which easily burns through the material. Laser cutting can be used on materials such as metal, aluminium, plastic, wood, rubber, etc. Lasers use computer numerically controlled programming (CNC) to determine the shape and position ls of the cutouts. Material thicknesses of up to 20mm can be lasercut. There are advantages and disadvantages in using lasercutting. CO2 lasers are more traditional, and can cut thicker materials but do not deliver such an accurate cut as fibre lasers. Fibre lasers can generally cut thinner materials and have much higher cutting speeds than CO2 .
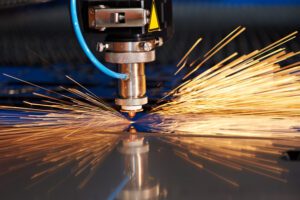
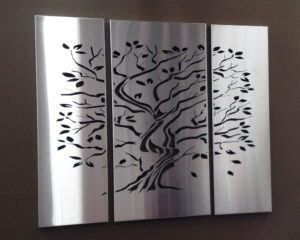
Tolerances
General Tolerances-If a drawing or specification sheet has not been provided by the customer, we will manufacture the product from the model to the specifications listed here. Sharp edges will be broken and deburred by default. Critical edges that must be left sharp should be noted and specified on a print.
- Material Restrictions
- Acceptable Materials
- Localized hardening
- Distortion
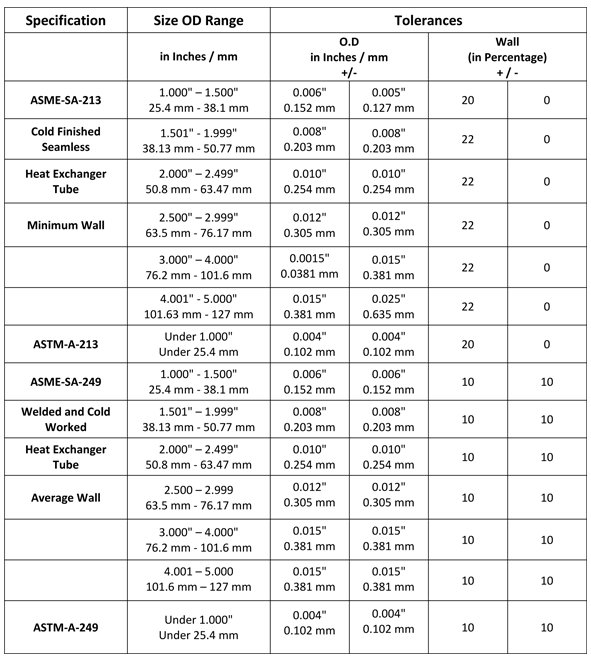
Features
Corner Fillets-Filleting or rounding the corners of sheet metal is done in order to provide a smooth finish. Fillets remove sharp corners making them easier to handle and preventing cuts and scratches’ fillet is usually designed to be ½ the material’s thickness and filleting makes parts more cost-effective.
Relief Cuts-Relief cuts help parts fall closer to design intent to avoid “overhangs” and tearing at bends. Overhangs become more prominent for thicker parts with a smaller bend radius, and may even be as large as ½ the material’s thickness. Tearing may occur when bends are made close to an edge.
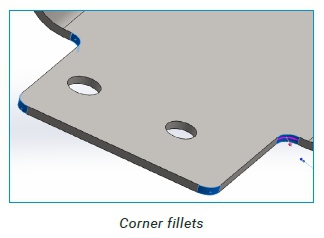
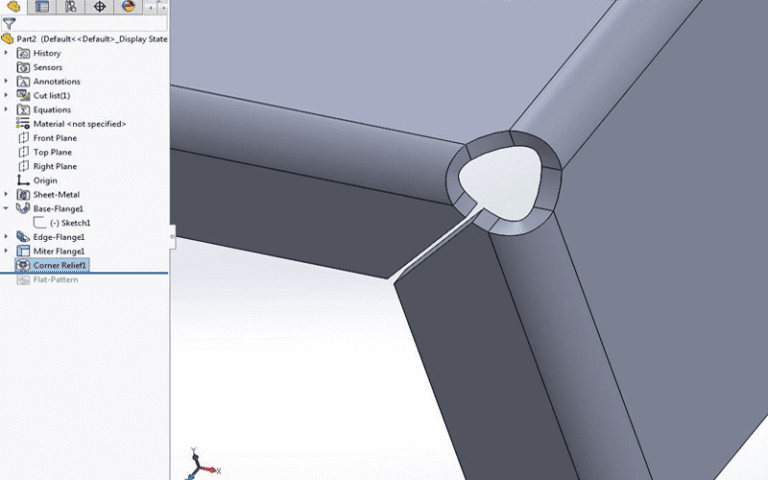
Upcoming Batches
Certifications
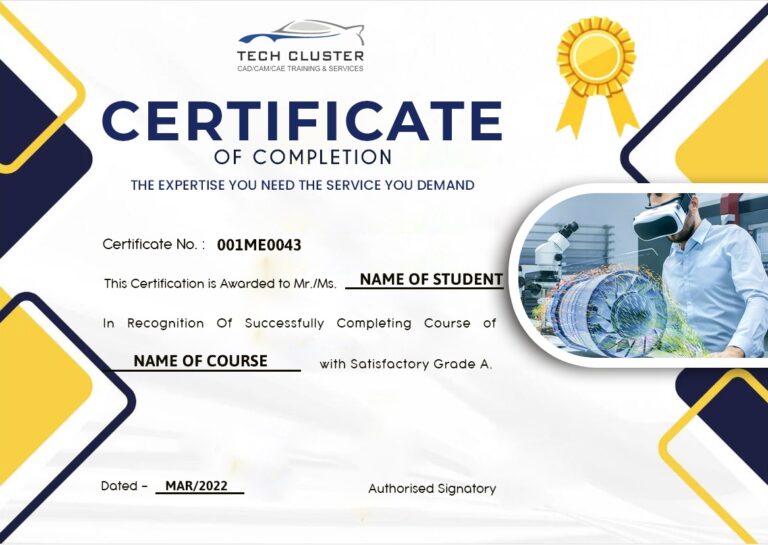
Sheetmetal Design Certification Training
About Sheetmetal Design Certification Training in Indore at Tech Cluster
Reviews
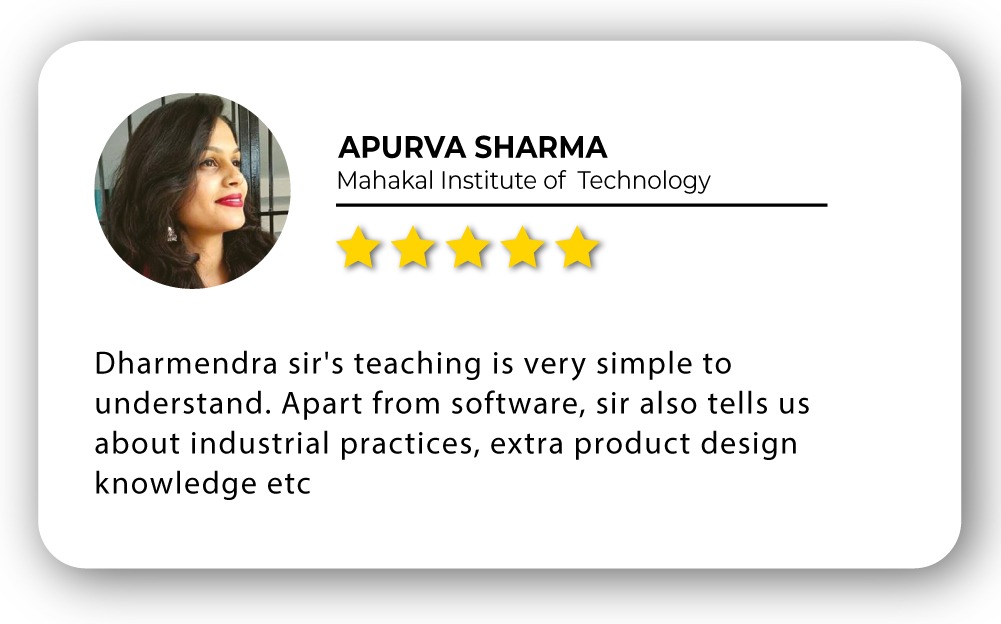
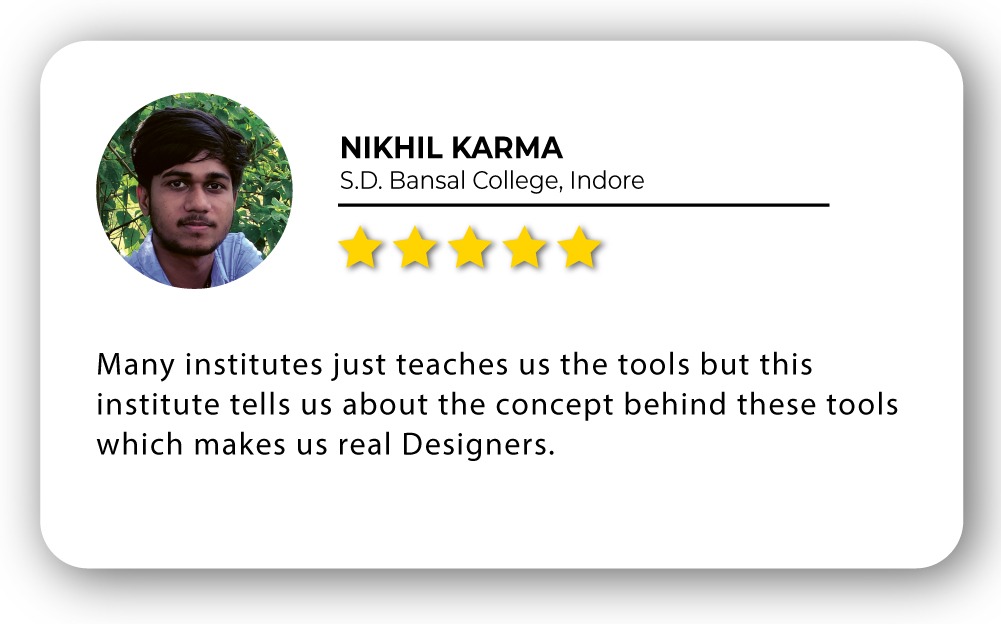
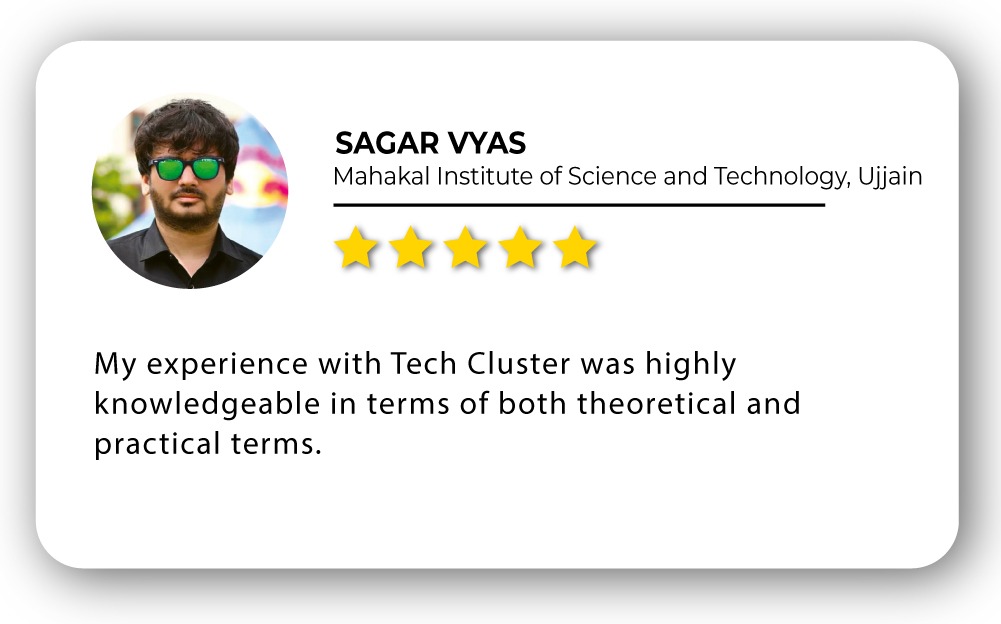