
CATIA Training Institute in India
- Real-Time Experts Sessions
- LIVE Project
- Certification
- Affordable Fees
- Flexibility
- Placement Support
CATIA is the short form of Computer Aided Three-dimensional Interactive Application.This application software is highly useful to the engineers, architects and all the folks who design machineries, structures, etc. It comprises of all the three important aspects of designing software: CAD, CAM and CAE.
This course is very beneficial for the engineering/ diploma students as it can help you to build your career in various fields. Catia is not only useful for students but also a very powerful software used by professionals in Automobile Industries for surfacing body shapes of all kinds of vehicles.
Choose one of the best Catia training centers in Indore to enhance your skills and career.
Tech Cluster is an institute in Indore with highly professional faculties with many years of industrial experience. To learn any tool it’s important to get your basics clear, which is why we are here to on-board you for the learning journey of Computer Aided Three-dimensional Interactive Application.
Applications
- For Mechanical Engineering: The use of CATIA enables the creation of 3D parts, provides technology for mechanical surfacing and provide tools for completing the product definition, which includes functional tolerance and kinematics definition.
- Design: Allows creation and modification of complex and innovative shapes and supports multiple stages of product design.
- For System Engineering: The CATIA is a proficient software which provides an open systems engineering development platform that enables simulation, modelling, business process support and verification.
- For Electrical Systems: CATIA provides solution for designing and manufacturing of electrical systems widely used across various industries. It includes the complete process that starts right from the top of conceptual designing up to complete manufacturing capabilities.
- Fluid systems: CATIA offers solution for designing and manufacturing complete layout for tubing, piping and Heating, Ventilating and Air Conditioning (HVAC)systems.
CATIA Course Highlights:
CATIA Foundation :
- Introduction of CATIA
- Sketcher
- Part Modelling
- Editing
- Surface Design
- Assembly Design
- Drafting & Drawing
- Geometric Dimensioning And Tolerances
Duration :
- 25 Hours Theory
- 25 Hours Practical
- 20 Hours Project work
Technical Features:
INTRODUCTION OF CATIA
- CAD/CAM/CAE Product cycle
- Parametric Technology
- Introduction to CATIA Environment & Menu bar and Use of Mouse

SKETCHER
- Profile Toolbar :- Different Types Of Profiles With CATIA Interface, Concept Of Parametric To Draw Profiles Like Line, Rectangle, Circle, Etc
- Operational Toolbar:- Sketching Techniques, Scaling, Copying, Moving, Rotating, Transfer, Offset, Etc.
- Constraints:- Definition, Dimensional Constraints Like Linear, Align, Geometric Constraints Like Horizontal, Vertical, Tangent, Etc With Respect To ISO Constraint, Under Constraint Or Over Constraints Geometry.
PART MODELING
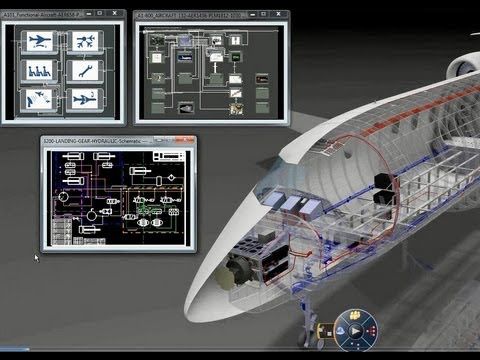
- Understanding Part Design Environment
- Creating Solid Models using Sketch-Based Features
- Working with Dress-Up Features
- View Toolbar
- Creating & Working efficiently on Reference Elements Planes and lines & points
EDITING
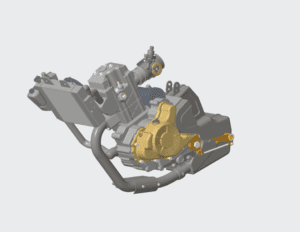
- Updating Features
- Transformation Features e.g. Patterning, Rotating
- Advanced Modeling Techniques e.g.
- Boolean Operations, Annotations, Assigning Materials & Measuring Properties.
SURFACE DESIGN
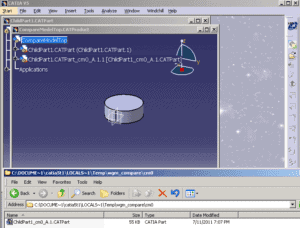
- Creating Wireframe elements e.g. helix, splines, Curves, etc.
- Creating Surfaces like blended, lofted surfaces, etc.
- Operations on Shape Geometry e.g. Joining, splitting & trimming.
- Advanced Task in which Surface Operations like Healing, Extracting, etc.
- Solidifying Surface Models:- Adding Thickness To A Surface Creating A Solid Body From A Closed Surface Body, Sewing A Surface To A Solid Body
- Advance Shape Morphing Tools, Sweep With Total 28 Types Of Sweep Profile, BIW Features Etc
ASSEMBLY DESIGN

- Bottom Up Assembly With Detail Explanations
- Top Down Assembly With Detail Explanations
➢ For Bottom Up Assembly
Assembly Constraints:- Static Constraints Like Mate, Align, Insert Etc Working With Package & Flexible Components With Exploded Representation As Per X, Y, Z Direction. Open Components In Separate Window For Constraint Creation,
➢ For Top Down Assembly
Assembly Constraints :- Static Constraints Required Mainly The Ref. Along Surfaces, Along Plane, Mainly It Is Use For Large Assemblies In Which Small Components Will Not Be Assembled By Constraints Easily.
DRAFTING & DRAWING
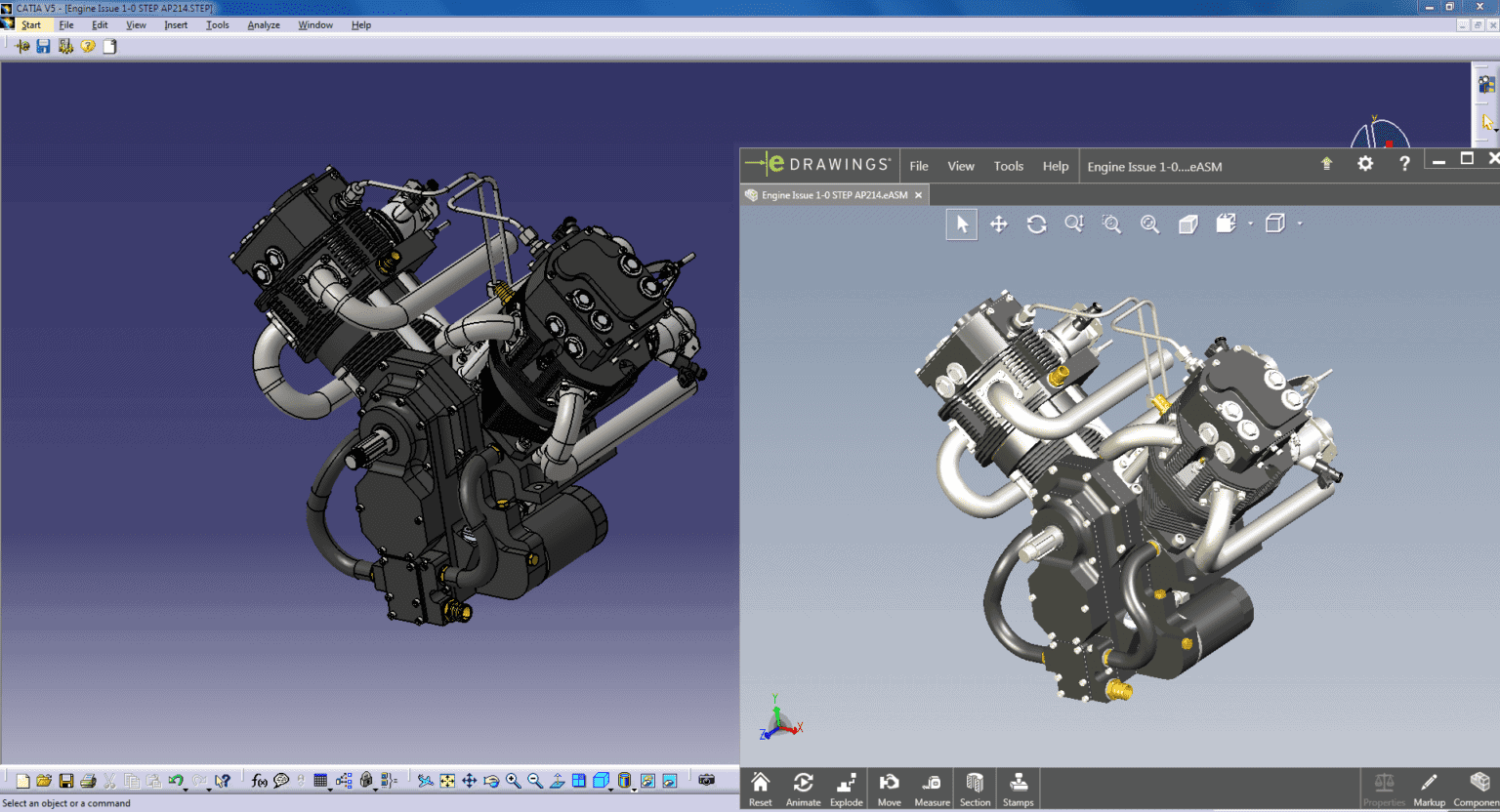
Introduction To Drafting, Drawing with Or Without Template, Formats, Placing General, Projection, Auxiliary, Prospective Views, Placing Dimensions, Overwriting the Dimensions, Etc
Types Of Drafting:-
- a) Generative Drafting with Detail Explanations – By Placing the Orthographic Projections in Sheet with Isometric View Which Is Mainly Use For Production In Manufacturing.
- b) Interactive (Detail) Drafting with Detail Explanations- By Placing the Whole Assembly with Exploded View by Creating Bill Of Material And Balloons Due To Which We Easily Assemble The Assembly In Assembly Line In Manufacturing
Geometric Dimensioning And tolerances
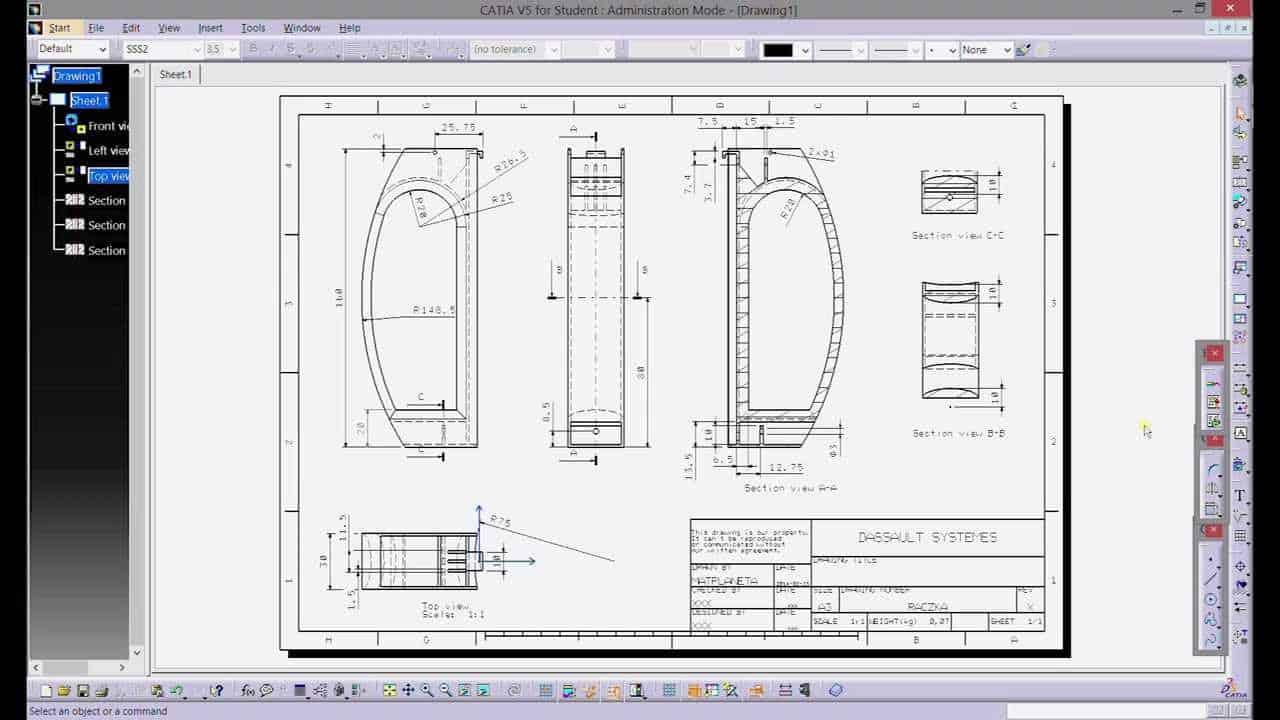
TECH CLUSTER Institute of Design Includes Fundamentals and Advance Concepts of Geometric Dimensioning and Tolerances In Accordance With ASME Standards.
- Introduction
- What Is GD&T?
- Why Should GD&T Be used?
- Feature Control Frame
- GD&T Symbols/Meanings
- Maximum Material Condition (MMC)
- Regardless Of Feature Size (RFS)
- Different types of tolerances
- Conversion Charts

Upcoming Batches
Certifications
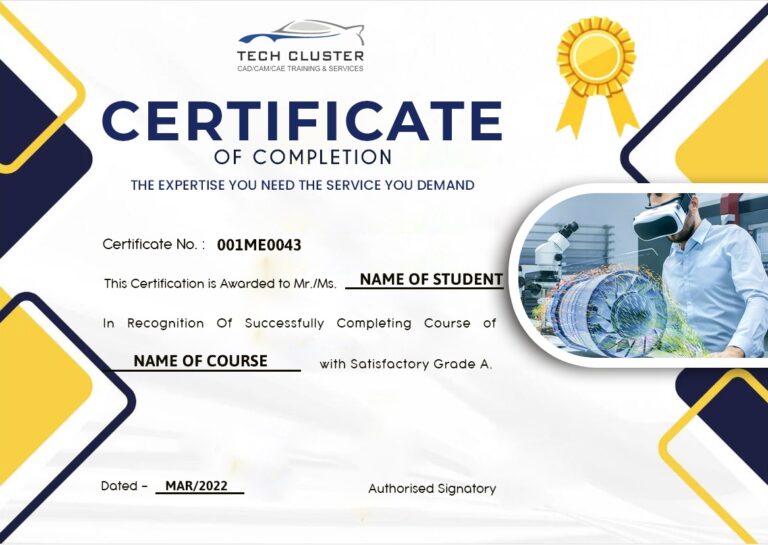
CATIA Certification Training
About CATIA Certification Training in Indore at Tech Cluster
Reviews
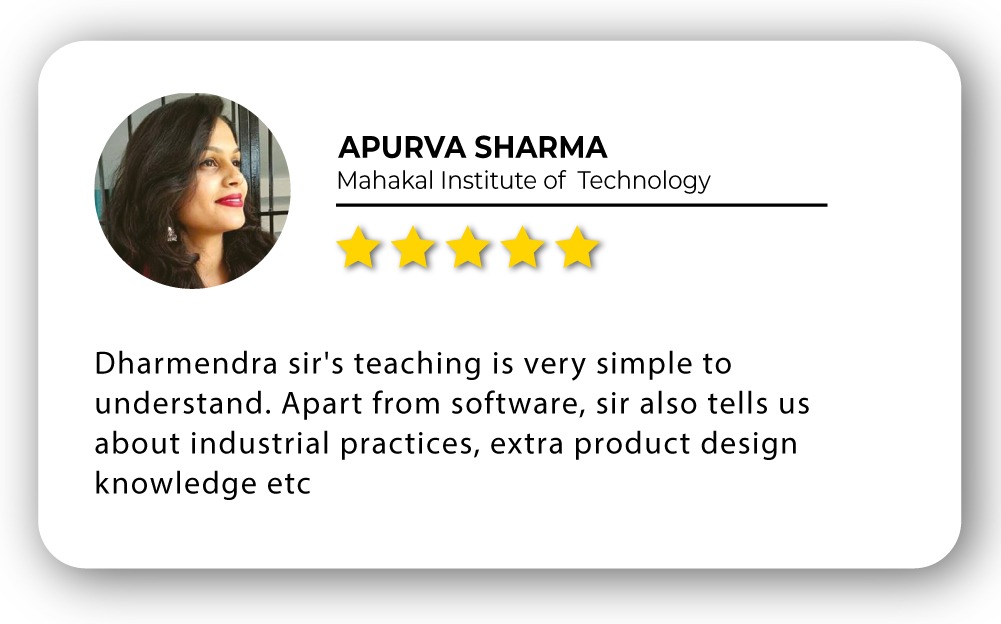
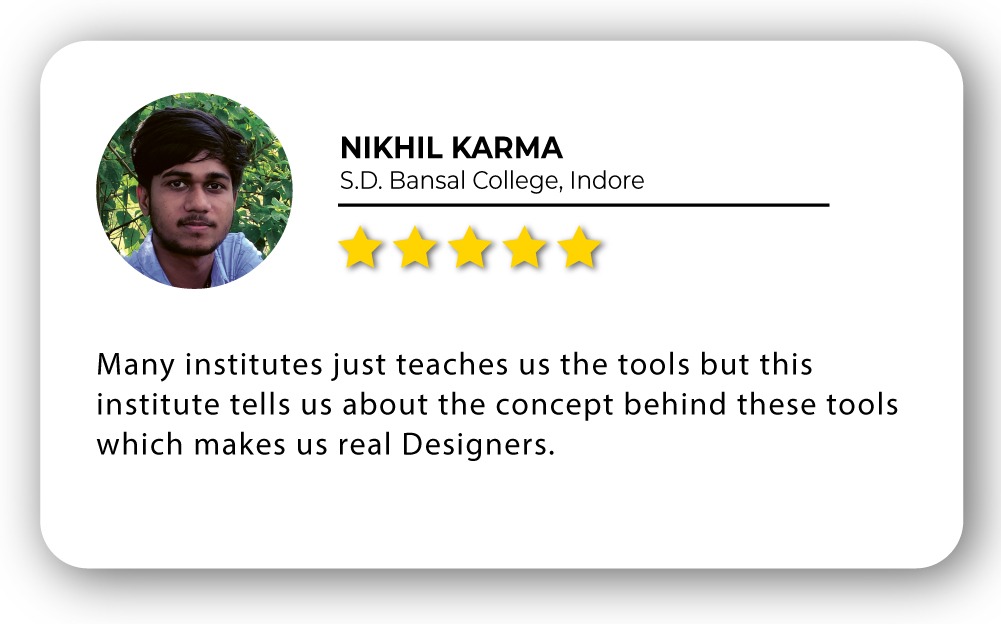
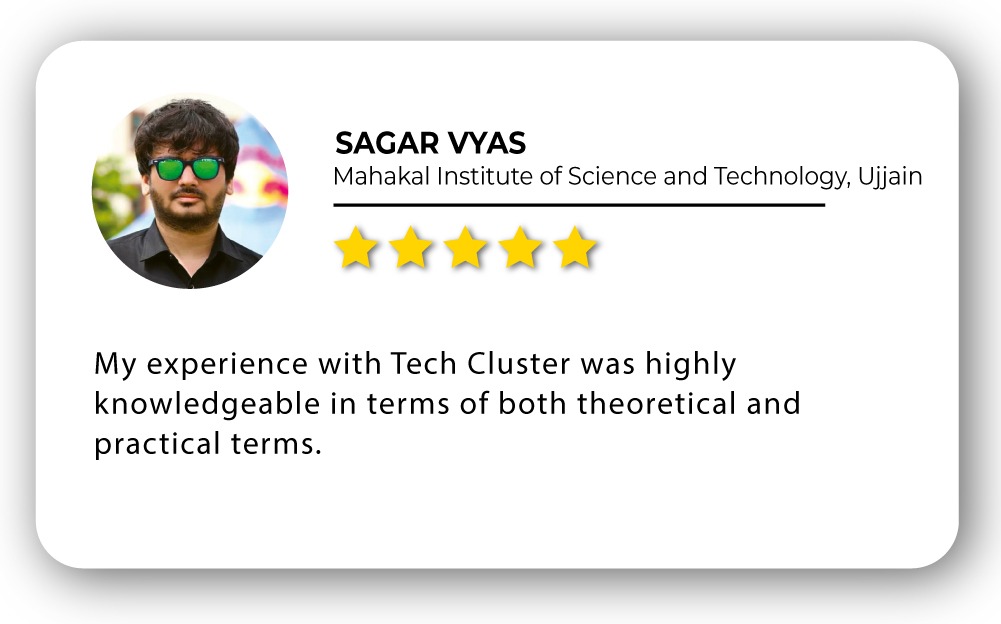